Maintenance Planning
Maintenance and upkeep activities are critical in any organization/company/industrial or technological factory.
By nature, these organizations rely on technological processes, equipment, and machinery from all disciplines, both during the design and establishment phase and during operations and day-to-day functioning.
Maintenance and care of the organization’s physical assets are a significant cost component throughout their lifecycle, yet traditionally, they do not receive the necessary attention and are often relegated to a low priority in the organization’s agenda.
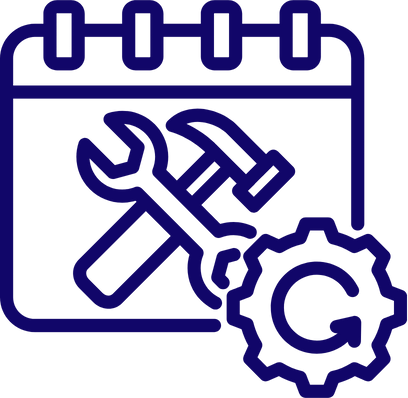
There are several main reasons why maintenance is not prioritized:
• The topic is not considered “sexy” and is seen as an inevitable chore (hence only the minimum necessary is done).
• There is insufficient awareness of the economic benefits of performing maintenance.
• There is no documentation or measurement of maintenance, making it difficult to see and quantify its operational benefits.
Neutral studies show that the correct use of planned maintenance and corrective maintenance techniques and tools can save about 10%-30% of an organization’s operational costs and provide additional benefits, such as improved reputation, reduced workplace accidents, employee satisfaction and more.
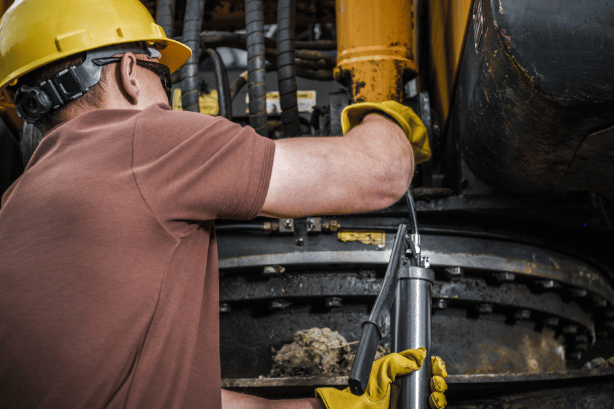
Throughout my professional career, I have been heavily involved in maintenance from all its aspects: as a planner, maintainer, and operator of systems and equipment.
It is a structured discipline, an engineering field in itself, requiring knowledge, experience, and a deep understanding of processes and relationships within an organization/company/factory.
Goal: To optimize and reduce maintenance costs for the organization/company/factory.
Method: Understanding the organization/company/factory, analyzing the current situation, defining availability goals, defining maintenance cost and savings targets compared to the current state and implementing a computerized maintenance management system (CMMS), if relevant.